Vacuum replica service
The tolerance is as low as ± 0.004 "(0.08mm)
Delivery within 1 day at the earliest
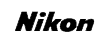
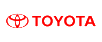
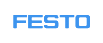
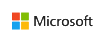
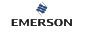
vacuum complex mould
YXD has a leading vacuum complex mold technology, using silicone molds to quickly replicate polyurethane castings similar to engineering plastics. It is an ideal choice for hand function testing and small batch production.

What is vacuum mold?
Vacuum mold, also known as silicone mold or hand mold, is an economical alternative to small batch injection molding of plastic parts. Usually, the mold uses CNC or SLA parts as a prototype, made of silicone material, and the parts are made of polyurethane PU material through the process of vacuum injection molding. The complex mold can accurately replicate the structure, details and texture of the prototype, and provide a surface finish consistent with the prototype, obtaining a result similar to that of injection molding.
Advantages of Vacuum Compound Mold
1. Cheap silicone mold, silicone compound molding process without investment expensive and time-consuming injection mold.
2. Wide selection of materials Polyurethane materials for vacuum injection molding can be rigid, flexible, transparent, and various colors.
3. Fast delivery 10 to 15 days can produce up to 50 with a certain function of the hand plate complex mold.
4. High precision and fine details The vacuum complex mold can provide high precision and high precision parts with production-level quality level.
5. Excellent surface finish Compared with CNC hand plate or 3D printing, vacuum complex mold can provide better surface quality.
Working principle of silicone compound mold
The manufacturing process of silicone compound mold is divided into three steps: making a prototype, making a mold and pouring parts.
Step 1: Prototype
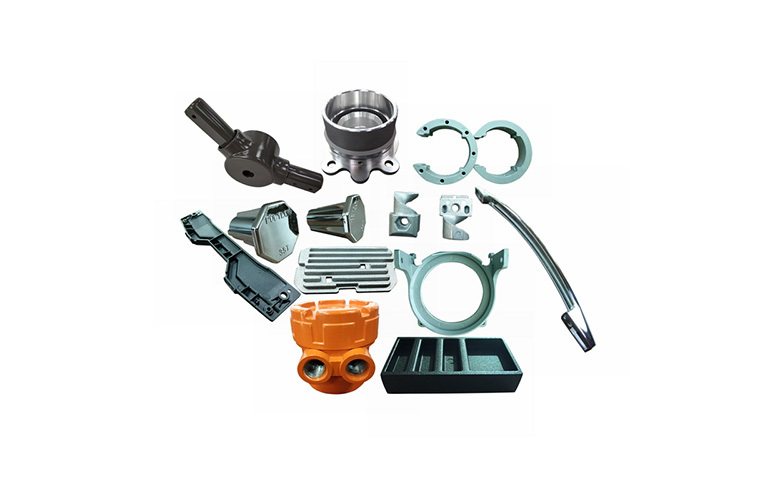
Step 1: Prototype
The quality of the complex part depends on the quality of the prototype. When you need to maintain high precision, high finish and even optical transparency, the prototype is best machined by CNC. In addition, for parts with complex shapes and structures, we will also consider using SLA to make prototypes.
We can spray texture or fog on the surface of the prototype to simulate the final mold texture of the product. The silicone mold will accurately replicate the details and textures of the prototype, and the surface of the final complex part will maintain a high degree of consistency with the prototype.
Step 2: making silicone mold
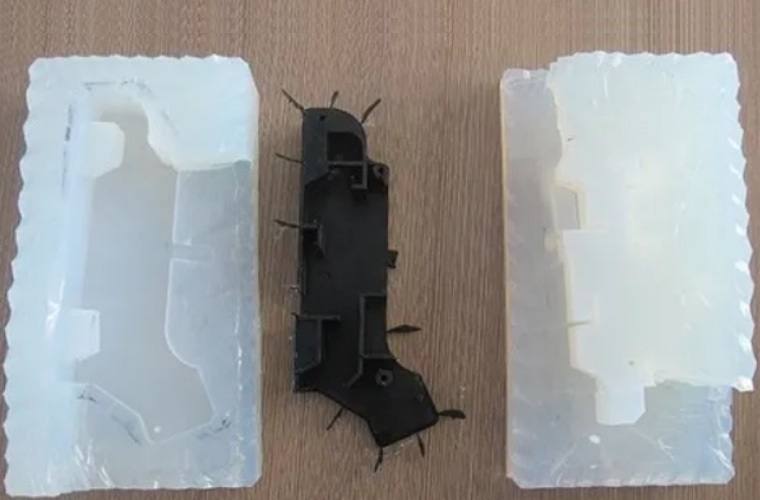
Step 2: making silicone mold
The casting mold is made of liquid silicone, also known as RTV mold. Silicone rubber is excellent in chemical stability, self-release properties and flexibility, which can minimize shrinkage and effectively copy part details from the prototype to the mold. The production steps of silicone mold are as follows:
Stick tape around the prototype in a flat position so that it is easy to open the mold later, which will also become the parting surface of the final mold.
· Hang the prototype in a box and place glue sticks on the parts to set the pouring port and exhaust holes.
· Inject silicone in the box and vacuum, and then cure it in the oven at a temperature of 40°C for 8-16 hours, depending on the volume of the mold.
· After the silicone rubber is cured, the box and the glue rod are removed, the prototype is taken out of the silicone, a cavity is formed, and the silicone mold is made.
Step 3: Vacuum Injection
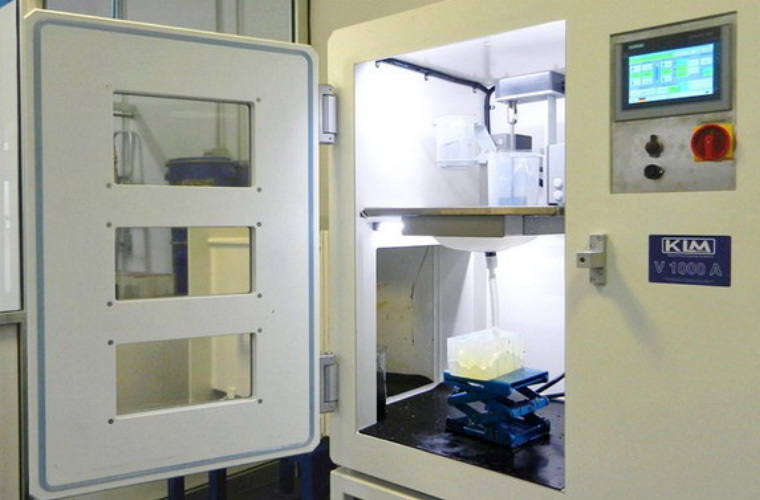
Step 3: Vacuum Injection
YXD standardized operating procedures ensure accurate part replication and consistent mechanical properties. Our technicians control all operating parameters: mixing, venting, stirring, preheating, pouring and demolding, providing near-perfect prototype copies. Vacuum injection molding process is as follows:
· First place the silicone mold in the oven and preheat to 60-70°C.
· Select the appropriate mold release agent and use it correctly before closing the mold, which is very important to avoid sticking to the mold and surface defects.
• Prepare the polyurethane resin, preheat it to about 40°C before use, mix the two-component resins in the correct proportions, and then thoroughly stir and degas under vacuum for 50-60 seconds.
• Pour the resin into the mold in the vacuum chamber and then cure the mold again in the oven. Average curing time: 1-3 hours for small pieces and 3-6 hours for large pieces.
• After curing the castings were removed from the silicone mold. Repeat this cycle.
Product Materials for Vacuum Fold
ABS(DPI8150, PX5118,PX200,PX600); ABS8150 high temperature resistance 70 degrees; PX223HT high temperature resistance 150 degrees; Soft rubber 8400 adjustable color; Transparent T387 transparent; Anti-flame retardant 8263; Transparent material: PC520 with blue color; Transparent material: PMMA5210; Translucent silica gel 905(35-40 degrees); Silicone 918; Transparent silica gel T-4(38-42 degrees); All transparent silica gel made; PP-like PP5690
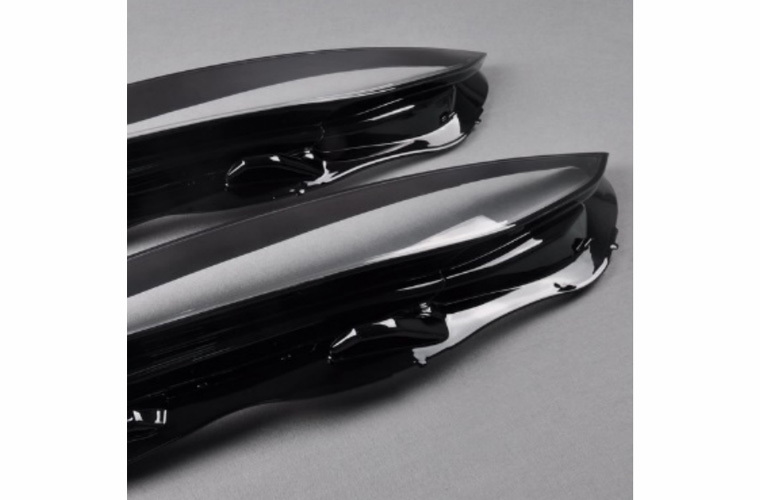
Replica product01
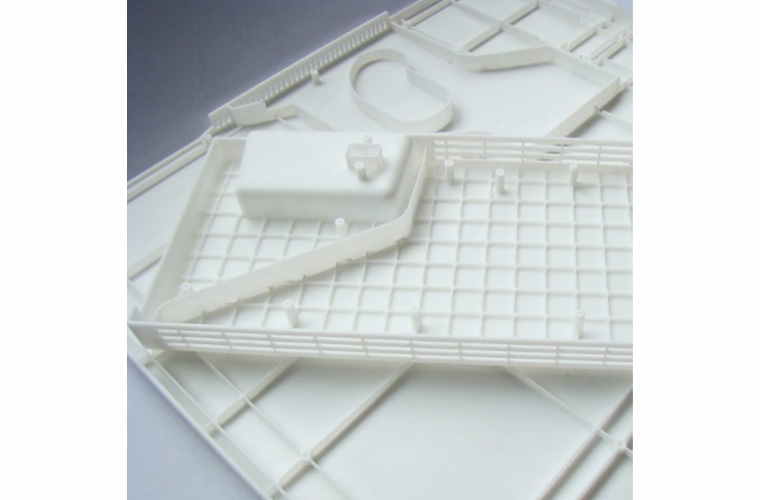
Replica product02
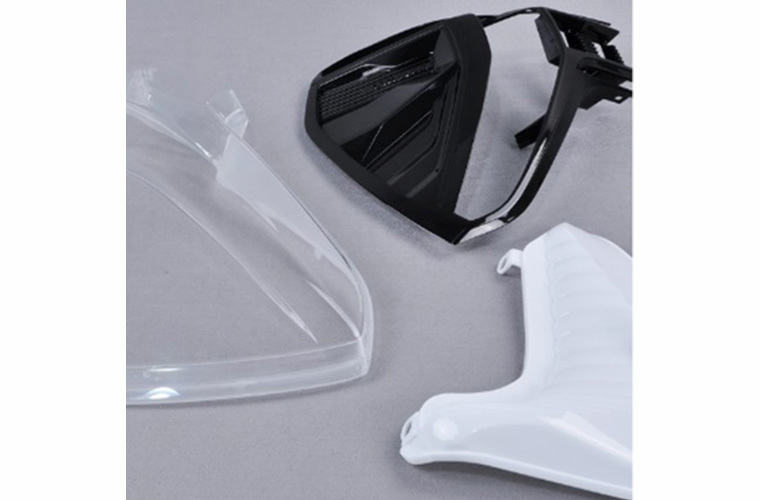
Replica product03
Application of Vacuum Compound Mould
Silicone compound molding is an effective method for small batch production of functional hand plates and plastic parts, and helps you strike a balance between high-quality production parts and the shortest delivery time.
Why Choose Our CNC Milling Services
With Youxingda's CNC milling services, you're investing in more than just machinery. You will have the promise of impeccable accuracy, a strict schedule and the support of experienced professionals.
Instant online quotation
No need to write a quote request email, just upload your design files to get an instant CNC quote. Ensure instant, detailed estimates tailored to your CNC milling requirements, eliminate guesswork and effectively launch your project.
Milling parts with strict tolerances
Experience unparalleled precision in every task. Our advanced milling processes ensure that components adhere to tight tolerances, accurate to ± 0.01mm, for seamless assembly and operational excellence.
Fast delivery time
Speed up your manufacturing cycle. Youxingda's domestic workshops and state-of-the-art machinery ensure fast turnaround times, helping businesses stay motivated and meet critical deadlines.
24/7 Engineering Support
No matter when and where you are, you can confidently navigate your CNC milling project. Our experienced experts provide insightful guidance every step of the way to optimize designs and maximize output quality.
We will work with you to ensure the complete program is successful. Whether you need hand models, custom equipment or mass-produced components, Youxenda can provide reliable and consistent results on time.