Die casting services
Tolerance as low as ± 0.004 '' (0.1 mm)
Powerful technical support
ISO 9001:2015 Certified Manufacturing Partner
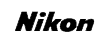
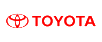
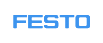
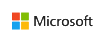
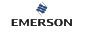
24h
Quick Quote
Period of 10 days
Delivery time
0pc
Minimum order quantity
0.010 mm
Tolerance
Our Precision Die Casting Services
If you need custom metal parts, Youxenda is a die casting service manufacturer that can help. Since 2009, we have been demanding that our engineering teams and equipment meet high standards for the continuous delivery of rugged parts and prototypes. To ensure legendary quality, we use a strict die casting process to ensure that your customization requirements are met. These are the two die casting capabilities we offer.

Cold chamber die casting
Cold chamber die casting process is a very important process that helps to reduce heat and solve the problems of machine plunder and corrosion of related components. This process is mainly used for high melting point alloys such as aluminum, magnesium, certain copper and iron alloys.

Hot chamber die casting
Hot chamber die casting, also known as goose neck casting, is a relatively fast process, with a typical casting cycle of only 15 to 20 minutes. It allows for the mass production of relatively complex parts. This process is suitable for low melting point alloys such as zinc alloys, lean alloys, and copper.
Why choose Youxingda to produce die castings
Strict quality control
We offer a wide range of possible material types, surface finish options, tolerances and manufacturing processes for your die castings. According to your customization needs, we provide you with different quotations and manufacturing recommendations so that you can get a personalized approach and the most cost-effective solution.
Powerful factories and facilities
We have established many of our own factories in China to ensure that your castings are manufactured with high efficiency and fast delivery time. In addition, our manufacturing capabilities take advantage of the latest automation facilities, which can support your various custom die casting projects, despite their complex design.
Strict quality control
We are ISO 9001:2015 certified company dedicated to providing precision die casting services. Youxingda's dedicated engineering team conducts strict quality checks at different stages of the manufacturing process: before production, during production, first article inspection and before delivery to ensure that the highest quality parts are manufactured.
Die casting from prototyping to production
Model
and cost-effective ways to create high-quality prototypes. The process utilizes low-cost tools, making it a cost-effective way to produce prototypes with a variety of materials and design changes.
Market testing
We help you create die-cast products suitable for market and consumer testing, concept models and user evaluations. Our die casting service allows you to quickly integrate changes for further testing and market launch.
On demand production
Die castings are a great choice for custom and first-run production. You can cost-effectively test product quality before starting full-scale production.
Technical standard for die casting
Dimensions
Standard
Minimum wall thickness
0.017 kg
Maximum part weight
12 kg
Minimum part size
∅ 17mm × 4mm
Maximum part size
300mm × 650mm
Minimum wall thickness
0.8 mm
Maximum wall thickness
12.7mm
Quality Control
ISO 9001 Data Security Certification
The smallest possible batch
1000 Piece Set
Alloys for the manufacture of die castings
Non-ferrous metals with low melting temperature can be used in die casting process, such as aluminum, zinc, magnesium, lead and copper. But some less common ferrous metals are also possible. The following will explain the characteristics of our common die-casting alloys for most parts.
Aluminum alloy
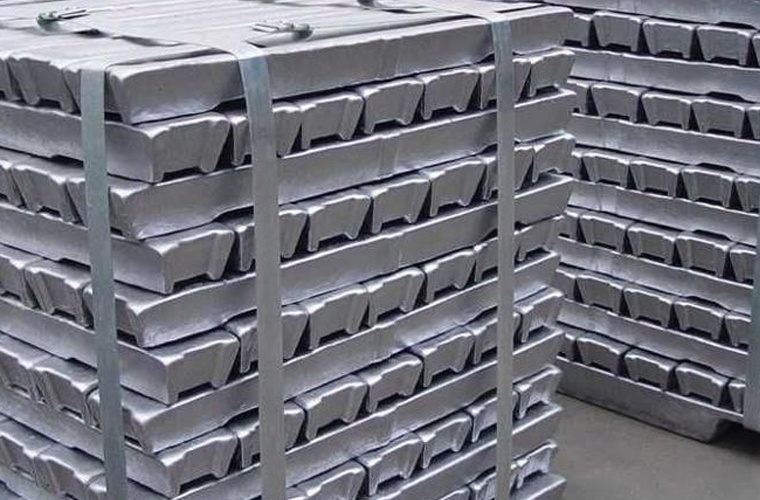
Aluminum alloy
Die casting aluminum alloy is a kind of lightweight structural metal, mainly containing silicon, copper, magnesium, iron, manganese, zinc and other elements.
With high thermal conductivity, electrical conductivity, cutting performance, linear shrinkage is small, so that it has excellent casting performance and filling ability.
Moreover, due to the low density and high strength, aluminum alloys can maintain good mechanical properties at high or low temperatures.
commonly used aluminum alloy:
A380、A360、A390。 A413、ADC-12、ADC-1
zinc alloy
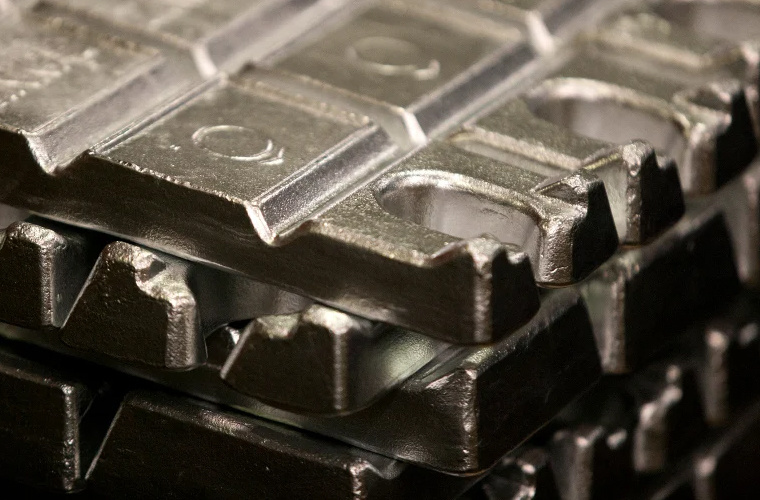
Aluminum alloy
The main elements added to the zinc die casting alloy are aluminum, copper and magnesium.
It provides a good surface finish without secondary processing. Importantly, zinc alloys are more cost-effective and stronger than other similar alloys.
In addition, it has better fluidity and corrosion resistance, so they are mainly used for die-casting meters, auto parts housings and other complex metal parts.
commonly used zinc alloy:
Zamak 2, Zamak 3, Zamak -5, Zamak -7, ZA-8, ZA-12, ZA-27
magnesium alloy
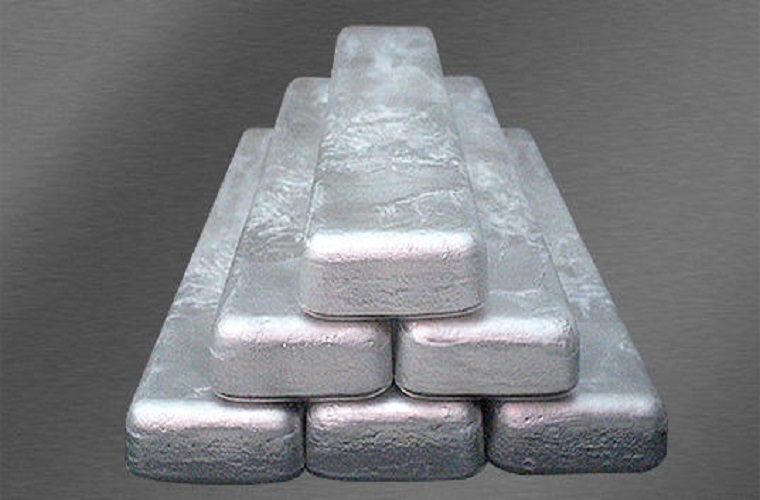
Aluminum alloy
The main elements added to the zinc die casting alloy are aluminum, copper and magnesium.
It provides a good surface finish without secondary processing. Importantly, zinc alloys are more cost-effective and stronger than other similar alloys.
In addition, it has better fluidity and corrosion resistance, so they are mainly used for die-casting meters, auto parts housings and other complex metal parts.
commonly used zinc alloy:
Zamak 2, Zamak 3, Zamak -5, Zamak -7, ZA-8, ZA-12, ZA-27
Die casting surface treatment
Post-processing and finishing are the last steps in precision die casting. Finishing can be used to remove surface defects of castings, enhance mechanical or chemical properties, and improve the appearance of products. There are six types of die cast surface finish options.
Name
Product Description
Materials
Color
Texture
Link

As an actor
Conventional casting surface treatment can be obtained without using high-end tools or machinery. Like zinc and aluminum zinc parts can be cast, but still maintain high corrosion resistance.
All Materials
Not applicable
Not applicable
/

powder coating
Powder coatings can be used to spray free-flowing dry powders to zinc alloy and aluminum alloy die castings. Under the action of strong static electricity and high temperature, the powder will be evenly adsorbed on the surface of the casting, forming a powder layer that can well cover the defects.
Aluminum, stainless steel, steel
Black, any RAL code or Pantone number
Gloss or semi-gloss

Sand blasting
Bead blasting is a process that uses compressed air as powder to spray fine glass beads onto the surface of die-casting parts at high speed. The appearance or shape changes, and the parts get excellent cleaning and surface treatment, which can be used for secondary finishing operations.
ABS, aluminum, brass, stainless steel, steel
Not applicable
Matte

anodic oxidation
Mainly used for aluminum alloy die casting. Anodic oxidation uses electrochemical principles to generate a layer of Al2O3 (aluminum oxide) film on the surface of the part. This oxide film decorative layer provides high insulation and wear resistance.
Aluminum material
Transparent, black, gray, red, blue, gold
Smooth, matte finish

electrophoresis
Used for aluminum alloy, zinc alloy die casting, etc. Electrophoresis gives castings a metallic luster, and the color range is not limited. It can also enhance the surface properties and corrosion resistance of metal alloy parts.
Aluminum, zinc, stainless steel
Unlimited
metallic luster
/

Electroplating
The plating may be functional, decorative or corrosion-related. This process is used by many industries, including the automotive industry, where chrome plating of steel automotive parts is common.
Aluminum, steel, stainless steel
Not applicable
smooth gloss

Polishing
Brushing is a surface treatment process in which an abrasive belt is used to draw marks on the surface of a material, usually for aesthetic purposes.
ABS, aluminum, brass, stainless steel, steel
Not applicable
Satin
Die Casting Applications
Die casting is a versatile manufacturing technology that plays an important role in the creation and production of many modern products, from aerospace structural parts to electrical enclosures. Youxingda offers innovative manufacturing solutions for different industrial applications. We provide high quality parts at competitive prices to important customers in the following industries:
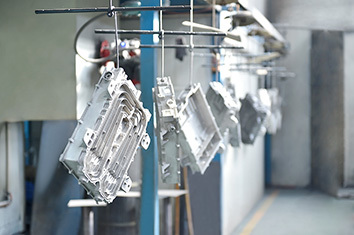
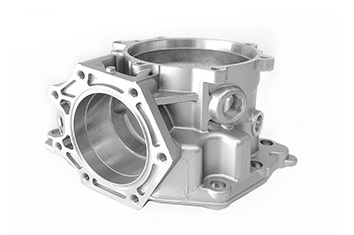
Auto parts: As a die-casting parts manufacturer, we focus on manufacturing auto parts, such as gears, cylinders, handwheels, transfer cases, small engine parts, and even parts for lawn and garden tractors.
Aerospace industry: Magnesium and aluminum die-casting technology from precision die-casting services can produce lightweight, durable structural components with strong corrosion resistance.
Lightning components: Our die-casting service is also suitable for electrical housings, die-cast radiators and more components.
Commercial and consumer goods: We also manufacture commercial parts, including compressor pistons and connecting rods, radiators, bearing housings, sink faucet parts, and meters.
Die Casting Gallery
View our informative gallery of precision die castings from our valued customers.
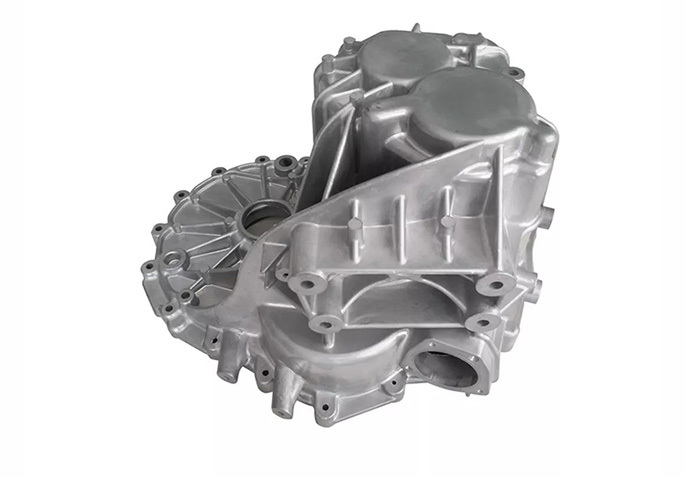
Die Casting Drawing Library01
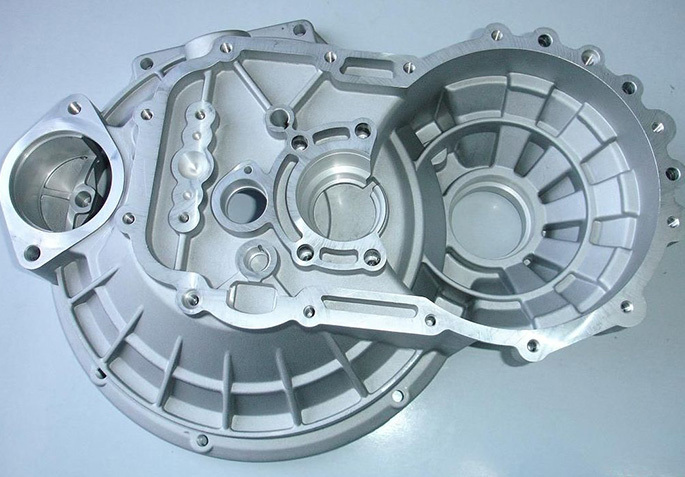
Die Casting Drawing Library02
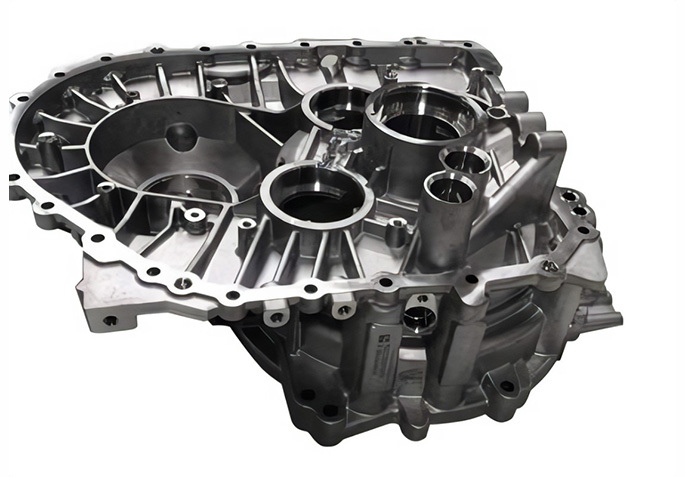
Die Casting Drawing Library03
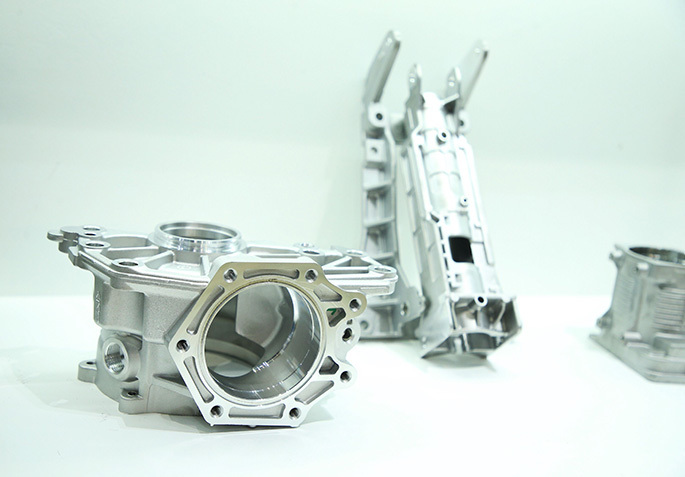
Die Casting Drawing Library04
Our die casting service in almost all industries
Youxingda partners with leading manufacturers from different industries to support growing demand and streamline their supply chain. Our digital custom die casting services help more and more manufacturers turn their ideas into products.